Organoclays
Organoclays being well dispersed within a suitable polymer are so small and their aspect ratio (L/D) is so high (> 500-1000) that material properties are improved at much lower loadings level than known from traditional fillers loadings. Nanocomposites do not show some disadvantages like higher density, brittleness, or loss of clarity compared to composites with conventional reinforcing fillers like talc or glass.
The organoclays most widely used so far in nanocomposites are natural minded and additionally modified montmorillonites supplied by Elementis, Nanocor and Southern Clay, all companies from USA. But also Süd-Chemie from Germany and Laviosa from Italy are offering such organoclays with different organic modifications. Table 1 shows a list of different companies using nanocomposites technology based on different nanofillers for their products.
It is well known that polyamide nanocomposites can be generated easily by extrusion and now more and more attention is focused to products based on commodity polymers like PE and PP. Nanocor's data in table 2 show up to 98% stiffness improvement in PP and higher heat deflection temperature (HDT). Important is also that the nanocomposite has virtually the same impact strength as unfilled PP homopolymer. General Motors announced an automotive production part based an olefinic nanocomposites. It's an exterior step assist for 2002 vans, made of a organoclay / TPO compound from Basell. Initially, the auto industry expressed most interest in polyamide nanocomposites for use under the hood, where higher heat deflection temperatures and lightweight were the goals. But one serious disadvantage for the polyamide nanocomposite compound was the loss of toughness in comparison to standard filled compounds. Therefore today, many automotive suppliers were interested in PP and TPO nanocomposites. But the generations of nanocomposites with these non-polar polymers are very difficult. New synthesis routes by pre-dispersed masterbatch versions or usage of modified polymers (maleic anhydride grafted polymers) are possible ways as reported by Dr. Lan from Nanocor. One further improvement for nanocomposites with high polymer processing temperatures (>260°C) is the usage of oligomer treated organoclays which avoids the unwanted thermally induced side-reaction of Hoffmann-elimination generating olefins from the quaternary ammonium compounds which are normally used as modifiers for montmorillonites.
PP Type, MFR |
Flexural Modulus, M Pa |
Heat Deflection Temp., o C |
Unmodified |
Nano-PP |
Unmodified |
Nano-PP |
Conventional 4g/10 min |
1145 |
2040 |
87 |
116 |
Conventional 14g/10 min |
1193 |
1779 |
86 |
109 |
Nucleated 35g/10 min |
1592 |
2310 |
113 |
126 |
Table 2: Effect of 6% Nano-Clay on PP Homopolymer Properties
Source: Nanocor |
The automotive producer Volvo has investigated 5 weight-% nanocomposites based on Basell's TPO modified with maleic anhydride as a coupling agent. Volvo observed 32 % to 50 % higher stiffness than 20 % talc-filled PP. Impact strength was lower than unmodified TPO but higher than 20 % talc-filled TPO. Volvo found that nanocomposite based TPO still has 68% lower stiffness than aluminum sheet.
A long-term goal for Dow Plastics is linked to reactor compounding of PP-nanocomposites using organoclays as catalyst support for in-situ polymerisation of PP homopolymers. Dow's activities are focused on highly loaded (up to 10% clay) PP-nanocomposites for semi-structural automotive uses. Nanocor has already developed a 40-50% organoclay based PP masterbatch. One reported potential use by Nanocor is for heavy-duty electrical enclosures that must meet various fire ratings plus demanding requirements for low temperature toughness and weatherability. Switching to PP-nanocomposites can result in 18 % weight savings and simultaneously less use of halogenated FR additives to reach a given UL rating. Recently Dr. Cogen from Dow Chemical Company reported that synthesized organoclays show very similar properties as natural occurring montmorillonites while having a white color compared to the beige color of the natural materials.
Kabelwerk Eupen from Belgium reported on several conferences melt blending of organoclays with EVA with important improvements to the wire and cable compounds. Cone calorimeter tests demonstrate dramatic decreases for the most important single fire hazard heat release. 3-5 weight-% loadings of the organoclays result in a 50-60 % reduction of the heat release (figure 2). It is important that EVA based nanocomposites only with the filler organoclay do not give enough flame retardancy. In a patent Kabelwerk Eupen claims that a filler combination of organoclays and traditional flame retardants like aluminum trihydrate or magnesium hydroxide must be used to fulfil the most important international cable fire tests like UL 1666 (riser test) or IEC 60332-3 cat A-D. As reported at different international conferences like Nanocomposites 2004 in Brussels it is now a general tendency to use such filler combinations (also with brominated flame retardants) to generate effective highly flame retardant compounds. For these developments Dr. Beyer from Kabelwerk Eupen received very recently 2 international research awards.
It is worth to notice that Kabelwerk Eupen AG regularly uses such cable compounds for the flame retardant cables. This is a very good example that nanocomposites have found their way to real products because Dr. Beyer reported the production of several hundred tons of nanocomposites based cable compounds per year for Kabelwerk's Eupen own cable productions.
Nanocomposites also show increased barrier properties by creating tortuous paths that slow the progress of gas molecules through the matrix resin (figure 3). At the same time, the dispersed organoclays are only few nm thick and therefore they do not interfere with the light resulting in transparent products. Consequently the major applications for polyamide-based nanocomposites today are high-barrier packaging for PET bottles, where the nanocomposites based layers demonstrate improved oxygen and carbon dioxide barrier properties. Honeywell offers a 2 % organoclay polyamide nanocomposite for bottles. At the conference ANTEC 2002 Honeywell summarized the benefits and requirements for polyamides based nanocomposites for the packaging industry:
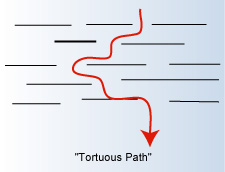 |
Figure 3: Mechanism of improved barrier properties by nanocomposites based on organoclays |
An early commercial use of nanocomposites as barrier film is a pasteurizable beer bottle that is introduced in China. Organoclays enhance also the stiffness of polyamide films. Honeywell claims that polyamide nanocomposites with 2 % organoclay has three times the oxygen barrier of virgin polyamides and 4 % organoclay demonstrate a six-fold improvement. That makes Honeywell's Aegis NC polyamide nanocomposites suitable for medium-barrier bottles and films with doubling of stiffness, higher HDT and improved clarity. Honeywell has turned its attention to create polyamide nanocomposites that can beat the cost of high-barrier plastics or even glass. Its current product is an active-passive barrier system called Aegis OX with organoclays for the passive barrier and polyamide specific oxygen scavengers as additional active additive. This combination results in a 100-fold reduction in oxygen transmission rate (OTR) versus the virgin Polyamide. Major PET bottle makers are testing aegis materials. Current barrier requirements for beer bottles (in which Aegis OX would be the core of a three-layer structure) set a maximum limit on oxygen ingress over 120 days, which is more than the average life time of the bottles circulation from filling stations to the usage by customers. Nanocor comes up with a different high-barrier option. Its Imperm compound improves the inherent gas barrier of amorphous MDX6 Polyamide from Mitsubishi Gas Chemical (both companies have formed a strategic alliance for this nanocomposites products) with the addition of an organoclay. As the central layer of a three-layer PET bottle, Imperm reported for the nanocomposite a 100-fold lower OTR than that of PET. Also stiffness of the nanocomposites is doubled and its gloss and clarity are similar to those of a costly high clarity co polyamide film. Meanwhile, nanocomposites also limit emissions of gasoline, methanol and organic solvents. Ube America developed nanocomposites based barriers for automotive fuel systems. It uses up to 5% organoclays for different polyamides. With 2% organoclay Ube reported that the corresponding nanocomposites are five times more resistant to gasoline permeation than unmodified polyamides. Ube has developed a co extruded barrier fuel line with the trade name Ecobesta, using PA 6/66 nanocomposite as the core layer. Ube reported at the conference Nanocomposites 2004 in Brussels the following advantages for fuel line based on Ecobesta-materials:
Structure: Multi-layer co-extrusion PA 12 + adhesive + PA6/66 nanocomposites + PA 6 with the following features:
- High speed extrusion
- Adhesive property
- Recycle performance
- Barrier property
- Cost reducti
Chasing the dream!
They are still in their infancy, but if the forecasts are right, nanocomposites could turn out to be the biggest little thing to hit plastics in decades. Polymers reinforced with as little as 2% to 5% of these particles via melt compounding or in-situ polymerization exhibit dramatic improvements in thermo-mechanical properties, barrier properties, and flame retardancy. They also can outperform standard fillers and fibers in raising heat resistance, dimensional stability, and electrical conductivity.
Dispersions of nano-scale reinforcements in polymers are already entering the marketplace in automotive and packaging applications, albeit in a low-profile manner and slower than had been anticipated. But that pace is expected to speed up dramatically, as indicated by the enthusiasm of researchers and marketers shown in roughly 200 papers delivered at three technical conferences. These were Nanocomposites 2004 in San Francisco, the SPE Antec 2004 in Chicago, and Nanocomposites 2004 in Brussels, Belgium A report from market-research firm Business Communications Co., Inc., Norwalk, Conn., pegs the total worldwide market for polymer nanocomposites at 24.5 million lb in 2003, valued at $90.8 million. It also projects the market to grow at an average annual rate of 18.4% to reach $211.1 million by 2008. Even if nano developments hit some snags, BCC says some applications will grow faster than 20% per year.
The leading nano-scale fillers in R&D and commercial projects are layered silicate nanoclays and nano-talcs, plus carbon nanotubes and graphite platelets. But other candidates are being actively investigated, such as synthetic clays, polyhedral oligomeric silsesquioxane (POSS), and even natural fibers like flax and hemp.
The top contenders
The two types of nano-fillers that have been most widely discussed and the first to break into commercial use are nanoclays and carbon nanotubes. Both must be chemically modified with surface treatments in order to achieve the fine dispersion and resins coupling that are required to derive maximum benefit.
Both of these nano-fillers have demonstrated improvements in structural, thermal, barrier, and flame-retardant properties of plastics. Carbon nanotubes also enhance electrical conductivity.
So far, nanoclays have shown the broadest commercial viability due to their lower cost—$2.25 to $3.25/lb—and their utility in common thermoplastics like PP, TPO, PET, PE, PS, and nylon.
The leading nanoclay is montmorillonite, a layered alumino-silicate whose individual platelets measure around 1 micron diam., giving them an aspect ratio of 1000:1. The two major domestic producers are Nanocor with its Nanomer line and Southern Clay Products with its Cloisite line. Both companies have formed alliances with suppliers of resins and surfactants, plus compounders and automotive OEMs and packaging firms. While much of their work is proprietary, they have disclosed several commercial successes.
General Motors has taken the lead in putting nanocomposites on the road. GM launched the first commercial auto exterior use of a nanocomposite in the step assist on the 2002 GMC Safari and Chevrolet Astro van. The part also appears on 2003 and 2004 models. More recently, a PP/nanoclay composite appeared on the body side molding of General Motors' highest-volume car, the 2004 Chevrolet Impala. GM's R&D Center in Warren, Mich., developed the compound in cooperation with Basell North America and Southern Clay Products.
The latest application is on the 2005 GM Hummer H2 SUT. The vehicle's cargo bed uses about seven pounds of molded-in-color nanocomposite parts for its center bridge, sail panel, and box-rail protector. The material is Basell's Profax CX-284 reactor TPO with nanoclay.
While nanoclay adds muscle to plastics, carbon nanotubes impart electrical and thermal conductivity. Nanotubes' commercial potential has been limited by their high price tags—reportedly in the range of $100/gram, although they are available in masterbatches for $50/lb and up. Still, nearly every car produced in the U.S. since the late 1990s contains some carbon nanotubes, typically blended into nylon to protect against static electricity in the fuel system. Static-dissipative compounds containing nanotubes are also protecting computer read/write heads.
Carbon nanotubes include both single-and multi-walled structures. The former have a typical outside diameter of 1 to 2 nm while the latter have an OD of 8 to 12 nm. They can range in length from the typical 10 microns to as much as 100 microns and have at least a 1000:1 aspect ratio. Carbon nanotubes have 50 times the tensile strength of stainless steel (100 GPa vs. 2 GPa) and five times the thermal conductivity of copper. When incorporated into a polymer matrix, they have the potential to boost electrical or thermal conductivity by orders of magnitude over the performance possible with traditional fillers such as carbon black or metal powders.
Domestic suppliers of nanotubes include Hyperion Catalysis with its Fibril multi-walled nanotubes and newcomer Zyvex Corp. with its NanoSolve single- or multi-walled tubes. Both suppliers now offer their products in
masterbatches that typically contain 15% to 20% nanotubes.
A different but related category is vapor-grown carbon nano-fibers from Pyrograf Products, a spin-off from Applied Sciences. Its Pyrograf III nano-fibers reportedly can compete with nano-tubes in providing thermal and electrical conductivity and dramatically enhancing mechanical properties and fire resistance (char formation). What's more, nano-fibers cost significantly less—around $100 to $150/lb. Evaluations are under way in nylon, PP, and polyurethanes.
Nanoclay compound sources
Alliances between Nanocor and two specialty compounders have resulted in commercial-scale nanocomposite concentrates and compounds for structural and barrier applications.
Noble Polymers new Forte PP nanocomposite compound made its commercial debut in the seat backs of the Honda Acura TL 2004 car. Forte replaced glass-filled PP, which caused processing difficulties, visual defects, and warping. Forte has a low density of 0.928 g/cc, superior mechanical properties, and improved surface quality and recyclability.
Noble reports that the Forte nanocomposite will also be used to produce the center console for a 2006 model light truck. Other applications in the works include office furniture—replacing 20% glass-filled PP—and appliance parts, where Forte reduces weight and possibly material cost.
PolyOne recently introduced the Maxxam LST line of PP homopolymer/nanoclay compounds that boast high stiffness and impact resistance. Through a patent-pending process, PolyOne reports that it has been able to overcome previous problems of incomplete exfoliation and dispersion of the nanoclay, resulting in performance that meets or exceeds many engineering thermoplastics. Lighter weight, aesthetic and processing advantages, and lower cost are also claimed.
PolyOne also offers Nanoblend concentrates of up to 40% nanoclay in homopolymer PP, modified PP, LLDPE, LDPE, HDPE, or an ethylene copolymer. Some grades are tailored specifically for barrier enhancement.
PolyOne reports that applications nearing commercialization include pallets
and dunnage, where Maxxam LST compounds are specified as alternatives to engineering resins due to their improved dimensional control, which is critical for robotic assembly. In addition, they boast good impact strength and lighter weight. Maxxam LST is also being considered for consumer disposable applications due to a combination of chemical resistance and stiffness, as well as dramatic cycle-time improvements.
Meanwhile, the Nanoblend concentrates are being considered for auto interior and exterior TPO parts. Key drivers are dimensional stability, lighter weight, and stiffness without loss of impact. Nanoblend concentrates are being evaluated in films for enhancing barrier, stiffness, HDT, and controlled release or migration of additives such as biocides and dyes. In blow-molded packaging, Nanoblend is being considered for improved barrier and the potential for thin walling and faster cycles. Thin-walling and faster cycles are also attractions in injection molded containers and totes. Some industry sectors are evaluating the concentrates for improving flame retardancy. |